Within the scope of numerous automotive megatrends, the reduction of pollutants and resource conservation plays an important role in the face of climate change and increasing individual mobility. The improvement in energy efficiency in electronic components is therefore allocated a wide area in the automotive development. A performance-optimized high-frequency (RF) wire is increasingly becoming a key element in the technological development of passive components, taking into account a weight-saving design and energy savings.
- Power electronics
- Driverless transportation systems
- Inductive battery charger
- Robotics
- Systems for braking energy recovery
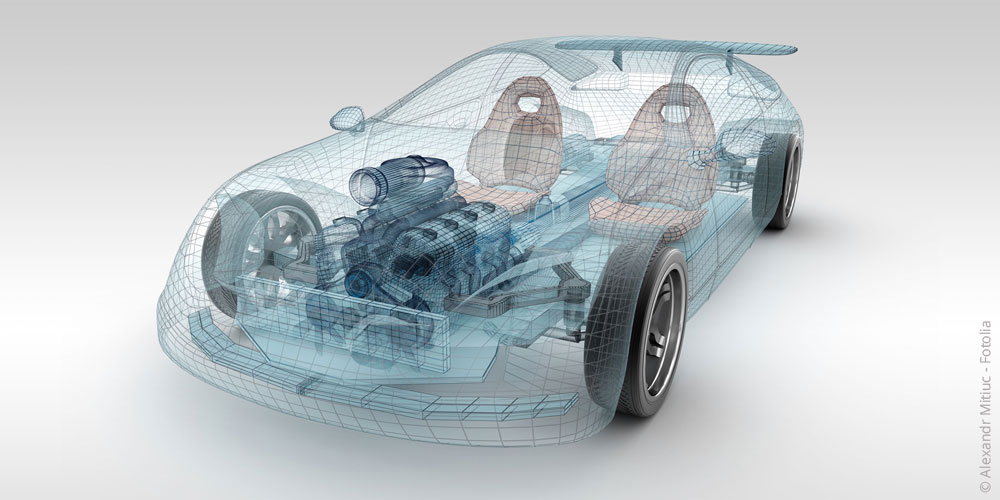
PACK offers performance-optimized HF strands for the automotive power electronics. As a reliable partner for well-known OEMs and Tear1, PACK supplies sustainable, individual and affordable solutions for prototyping, pre-production or serial production as industrial partners. The products meet the highest demands in terms of quality and reliability. PACK manufactures exclusively at its production site in Germany. With more than 80 years of manufacturing know-how in the areas of stranding, bandaging, winding, profiling and assembly, PACK is ideally equipped to transform the ideas of its customers into mature product solutions. A high production depth enables rapid sampling according to individual requirements.
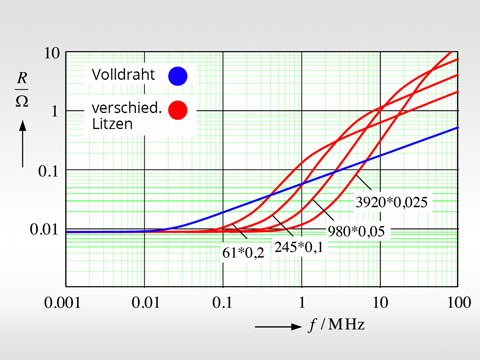
Loss resistors of strands with different number of cores and simultaneously the same total copper cross section In regular cooperation with universities such as the Nuremberg University of Applied Sciences, Faculty for Electromagnetic Fields at the ➔ Friedrich-Alexander University Erlangen-Nuremberg, scientific findings are put into practice.
In the framework of joint research projects, the electrical properties of HFLitz Wires are permanently optimized. These findings lead to new designs of HF strands with which the electrical losses in the windings of inductive components can be reduced. A sophisticated production control leads to the optimization of the skin effect, the inner proximity effect and the external proximity effect. The individual parameterization with respect to e.g. the number of cores, the outer diameter, the sling length, taking into account the frequency, voltage and other component specifications, is made possible by using Pitz's Optiscale © litz database.
Within the framework of the 5th Energy Research Program of the Federal Government "Innovation and New Energy Technologies", the companies Rudolf PACK and the Faculty for Electromagnetic Fields at the ➔ Friedrich-Alexander University Erlangen-Nuremberg, together with the transformer producer STS Spezial-Transformatoren-Stockach GmbH & Co KG. The aim was to optimize the windings in the transducer inductances. The results of this research project have been published in some specialist publications (including IEEE). A special print from the current electronics SH Power magazine with the most important results can be supplied directly from us.
Connecting enamelled copper wires or litz wires is always a challenge. Conventional tin plating often reaches limits in particular in automotive applications. PACK develops with special suppliers. For welding technology solutions for the optimal ‘contacting’
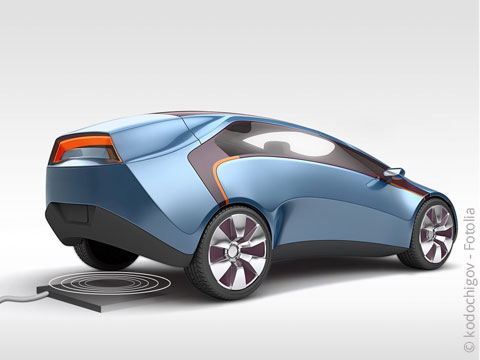
The security of supply and comfort play an important role in the implementation of electromobility as a mobility solution. The inductive charging as a cable-free battery charging technology proves to be an ideal solution.
In cooperation with a well-known OEM, all phases of component development (prototyping, freeze design, SOP, redesign) were carried out for an integrated charging pad. Typically, no norms or technical performance standards existed at the time of the development of this new technology.
In intensive cooperation, various prototypes were developed and in various series of tests the HF-comb combinations used were brought to serial production. Special attention was given to the exhaustion of the complete material competency of Pack with regard to strand insulation and the possible use of aluminum.